Complete Guide to Abrasives: Types, Uses & Maintenance
Abrasives are materials used for grinding, polishing, and surface finishing in various industries. They help shape, smooth, and clean surfaces in metalworking, woodworking, automotive, and construction. Choosing the right abrasive improves efficiency and ensures the best results.
Types of Abrasives
Abrasives are generally classified into two main categories: natural and synthetic.
Natural Abrasives
Natural abrasives are obtained from naturally occurring minerals and stones. These abrasives have been used for centuries and are still utilized in certain applications today.
Examples of Natural Abrasives:
- Emery – A mixture of aluminum oxide and iron oxide, used for polishing and metal finishing.
- Garnet – Commonly used in sandpaper and blasting applications, particularly for wood sanding and waterjet cutting.
- Pumice – A lightweight abrasive used for polishing wood, soft metals, and delicate surfaces like glass.
- Quartz – Used in sandblasting and surface preparation, particularly for cleaning metal and stone.
When to Use Natural Abrasives:
- When working with softer materials like wood and plastic.
- When a gentle finish is required, such as in furniture polishing.
- For eco-friendly applications, as natural abrasives are less harmful to the environment.
Synthetic Abrasives
Synthetic abrasives are engineered materials that offer superior hardness, uniformity, and durability compared to natural abrasives. These abrasives are widely used in industrial and commercial applications.
Examples of Synthetic Abrasives:
- Aluminum Oxide – One of the most commonly used abrasives, known for its toughness and durability. Ideal for sanding discs, grinding wheels, and metalworking applications.
- Silicon Carbide – A sharper but more brittle abrasive, excellent for cutting and finishing hard materials like glass, ceramics, and stone.
- Ceramic Abrasives – Offer high durability and are used for aggressive grinding and cutting applications.
- Diamond Abrasives – The hardest known abrasive, primarily used for precision grinding and cutting in high-performance applications.
When to Use Synthetic Abrasives:
- When working with hard materials such as metal, stone, and ceramics.
- For industrial applications requiring high durability and efficiency.
- In precision work, where uniformity and hardness are essential.
Common Applications of Abrasives
Abrasives are widely used across multiple industries. Below are some specific use cases where abrasives play an essential role.
Metalworking
- Grinding and shaping metal parts – Ideal for fabricators, machinists, and welders who need to refine and finish metal components.
- Surface finishing and polishing – Used in automotive and aerospace industries to create smooth and reflective metal surfaces.
- Rust and paint removal – Necessary for restorations and maintenance work, ensuring a clean surface before applying new coatings.
Woodworking
- Sanding and smoothing wooden surfaces – Essential for furniture making, cabinetry, and flooring preparation.
- Preparing surfaces for painting or staining – Ensures a smooth, even finish for better adhesion of coatings.
Automotive Industry
- Refinishing car surfaces – Helps restore old paint jobs and smooth out imperfections.
- Removing old paint and coatings – Used in body shops to prepare vehicles for repainting.
- Polishing for a high-gloss finish – Ensures a sleek and attractive final look.
Construction and Stonework
- Cutting and shaping stones – Essential for masons and tile workers.
- Polishing concrete and tiles – Common in flooring and countertop production.
- Surface preparation for coatings – Helps in ensuring adhesives and sealants bond properly.
Different Forms of Abrasives
Abrasives come in various formats, each suited for specific tasks:
- Sanding Discs – Used with power sanders for efficient material removal and surface smoothing, ideal for wood, metal, and auto bodywork.
- Sanding Belts – Commonly used in belt sanders for heavy material removal, ideal for woodworking and metal grinding.
- Sanding Sheets – Flexible and manually used for hand sanding or attached to orbital sanders for detailed work.
- Grinding Wheels – Designed for aggressive material removal, sharpening tools, and metal grinding.
- Abrasive Brushes – Used for deburring and surface finishing in metal and woodworking applications.
How to Choose the Right Abrasive
Choosing the correct abrasive depends on several factors, including the material being worked on and the desired finish. Here are some key steps to help in selecting the best abrasive:
Step 1: Determine the Material
Different abrasives work best for specific materials:
- Aluminum Oxide – Best for metals, wood, and general-purpose sanding.
- Silicon Carbide – Suitable for hard materials like glass, stone, and ceramics.
Step 2: Select the Grit Size
- Coarse grits (40-80) – Ideal for heavy material removal.
- Medium grits (100-180) – Used for smoothing and shaping.
- Fine grits (200-600) – Best for polishing and finishing.
Step 3: Choose the Right Format
Selecting between sanding discs, belts, sheets, or grinding wheels depends on the tool being used and the type of work required.
Important Considerations When Using Abrasives
- Always wear protective gear such as gloves and safety glasses.
- Use the appropriate speed and pressure to avoid overheating and damaging the surface.
- Ensure proper ventilation when working with fine abrasive dust.
- Regularly inspect abrasive tools for wear and tear.
How to Maintain Abrasives
Proper care and maintenance of abrasives extend their lifespan and improve efficiency.
Storage Tips:
- Store in a dry, cool place to prevent moisture damage that can weaken abrasives.
- Keep sanding discs and belts flat to avoid warping.
- Avoid extreme temperatures that can cause the abrasive material to degrade.
Cleaning and Maintenance:
- Use a rubber cleaning stick to remove debris from sanding belts and discs, extending their usability.
- Compressed air can help blow dust out of sanding sheets and pads.
- Wash waterproof abrasives (such as certain Silicon Carbide sandpapers) with water and let them dry completely before reuse.
- Avoid excessive pressure when using abrasives to prevent premature wear.
Conclusion
The most common abrasives include Aluminum Oxide and Silicon Carbide, both widely used in sanding discs and various industrial applications. Whether you are working with wood, metal, or ceramics, choosing the right abrasive is essential for achieving the best results. Before purchasing, consider the material, grit size, and format for optimal performance.
If you are looking for high-quality abrasives, visit our website! Abrasives Master has been a trusted supplier for over 10 years, providing top-grade abrasives with expert guidance. Explore our collection and find the perfect abrasive for your project today!
Continue Reading
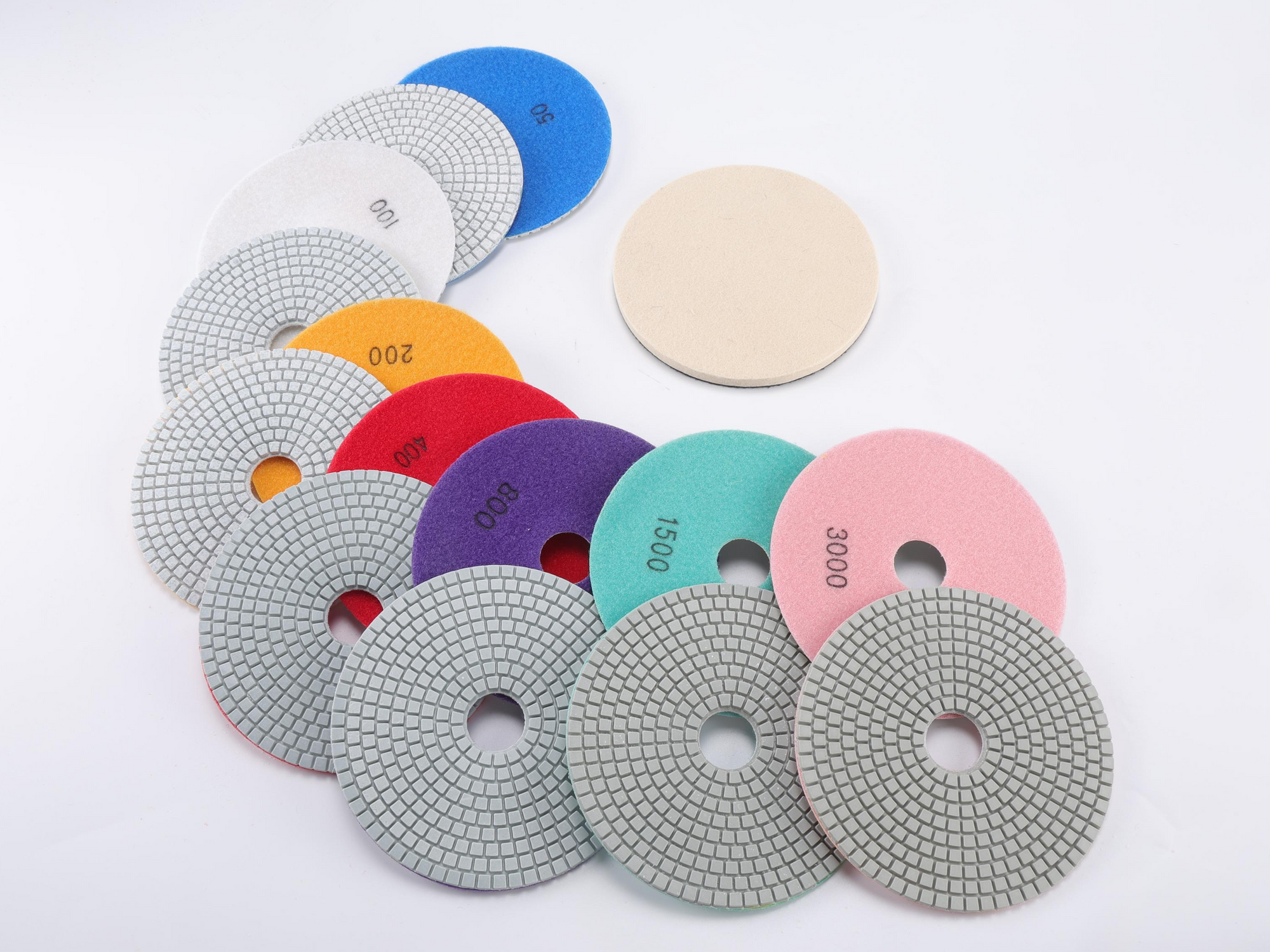
How to Polish Granite Using Diamond Polishing Disc
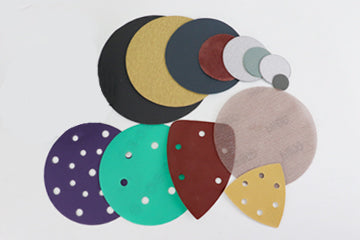