What Tests Should Be Performed on Abrasive Wheels? | Ring Test Guide
What Tests Should Be Performed on Abrasive Wheels? | Ring Test Guide
Abrasive wheels are essential in industries like metalworking and construction, offering durability and efficiency for cutting, grinding, and polishing. However, regular testing is necessary to ensure both performance and safety.
This guide outlines key tests that should be performed on abrasive wheels, including the ring test, to prevent failures and workplace hazards.
Preparing for Testing
Before performing any tests, it's important to take a few preparatory steps to ensure accuracy and safety:
- Inspect the wheel: Check for visible cracks, chips, or other irregularities.
- Clean the wheel: Remove dust and debris that could interfere with testing.
- Wear protective gear: Use gloves and safety glasses to prevent injuries.
- Ensure a safe environment: Perform tests in a stable and quiet area to avoid external disturbances.
What Tests Should Be Performed on Abrasive Wheels?
Ring Test
The ring test helps detect cracks in an abrasive wheel by tapping it lightly and listening to the sound it produces. A clear ringing sound indicates the wheel is intact, while a dull sound suggests a defect. This test should be done before mounting a wheel. Think of it like tapping fine porcelain—if it’s cracked, the sound will be dull instead of sharp.
Balance Test
An unbalanced wheel can cause excessive vibration, reducing precision and increasing machine wear. To conduct this test:
- Mount the wheel on a balancing device.
- Rotate it slightly and check for uneven weight distribution.
- If imbalance is detected, adjust or replace the wheel as necessary.
Like balancing a car tire, this ensures smooth operation and reduces stress on machinery.
Hardness Test
This test determines how well the wheel resists wear and deformation. A hardness tester applies force to the surface to evaluate its resistance level, ensuring the wheel is suitable for the intended application. Softer wheels wear faster but cut aggressively, while harder wheels last longer but may grind slower.
Tensile Strength Test
Abrasive wheels must withstand operational stress without breaking. This test measures the wheel’s resistance to tension by applying force until it fractures, ensuring it meets safety requirements. If a wheel fails this test, it should not be used as it may shatter under high-speed operation.
Diameter Test
Wheels must match the specified size for safe operation. The diameter test involves:
- Measuring the wheel using a caliper or gauge.
- Ensuring it complies with manufacturer specifications.
- Rejecting wheels that are significantly oversized or undersized, as they can affect performance and safety.
Why Is the Ring Test So Important?
The ring test is a quick and simple method to detect hidden cracks. A damaged wheel can break during operation, posing serious safety risks. Conducting this test helps prevent workplace accidents and ensures only defect-free wheels are used.
What Equipment Is Needed for a Ring Test?
To perform a ring test, you need:
- A non-metallic tapping tool (wooden mallet or plastic hammer)
- A stable support system
- Personal protective equipment (PPE)
- A quiet environment for accurate sound assessment
Steps to Perform a Ring Test
Understand Wheel Material and Suitability
Not all abrasive wheels are suitable for this test. Resin-bonded or organic wheels may not produce a clear ringing sound.
Suspend the Wheel
Place the wheel on a non-metallic surface or hang it securely so it can move freely.
Tap the Wheel
Gently tap the wheel in multiple spots along its outer edge.
Listen to the Sound
A clear ringing sound means the wheel is intact; a dull sound indicates cracks, and the wheel should not be used.
Common Mistakes and Misconceptions in Testing
Even with proper testing, errors can occur. Here are some common mistakes to avoid:
- Using metal tools for the Ring Test: This can distort the sound and lead to misinterpretation.
- Testing on a dusty or contaminated wheel: Dirt can absorb sound, making a good wheel seem defective.
- Ignoring balance issues: Even if a wheel passes the Ring Test, an unbalanced wheel can still be hazardous.
- Assuming all wheels require the Ring Test: Some bonded wheels do not produce a ringing sound and require other inspection methods.
What to Do If a Test Fails?
If a wheel fails any of the tests, take the following actions:
- Ring Test failure: Discard the wheel immediately to prevent potential breakage.
- Balance Test failure: Adjust the mounting or replace the wheel if necessary.
- Hardness or Tensile Strength failure: Contact the manufacturer, as the wheel may not meet safety standards.
- Diameter Test failure: Use only properly sized wheels that meet specifications.
Conclusion
Regular testing of abrasive wheels is crucial for safety and performance. The ring test, along with other evaluations like balance, hardness, and tensile strength tests, ensures reliability and prevents hazards.
At Abrasives Master, we prioritize quality and safety. Our abrasive wheels undergo rigorous testing to meet ISO quality standards, ensuring durability and performance. We also provide detailed usage guides and expert support to help you choose the right wheel for your needs. If you're unsure which wheel suits your application, contact us for professional recommendations.
Continue Reading
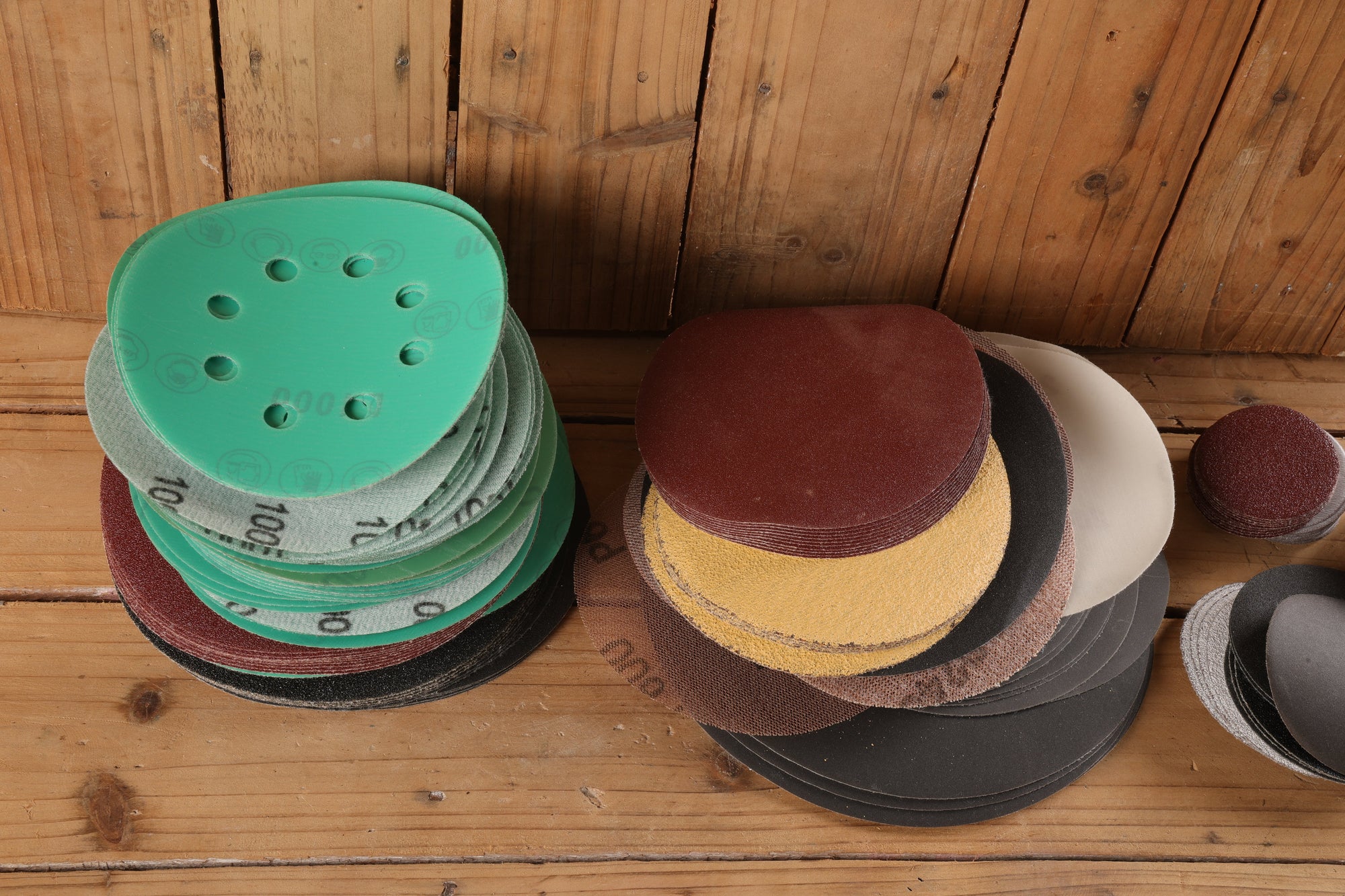
Understanding the Different Sanding Disc Backings – Cloth, Film, Hook & Loop, and PSA
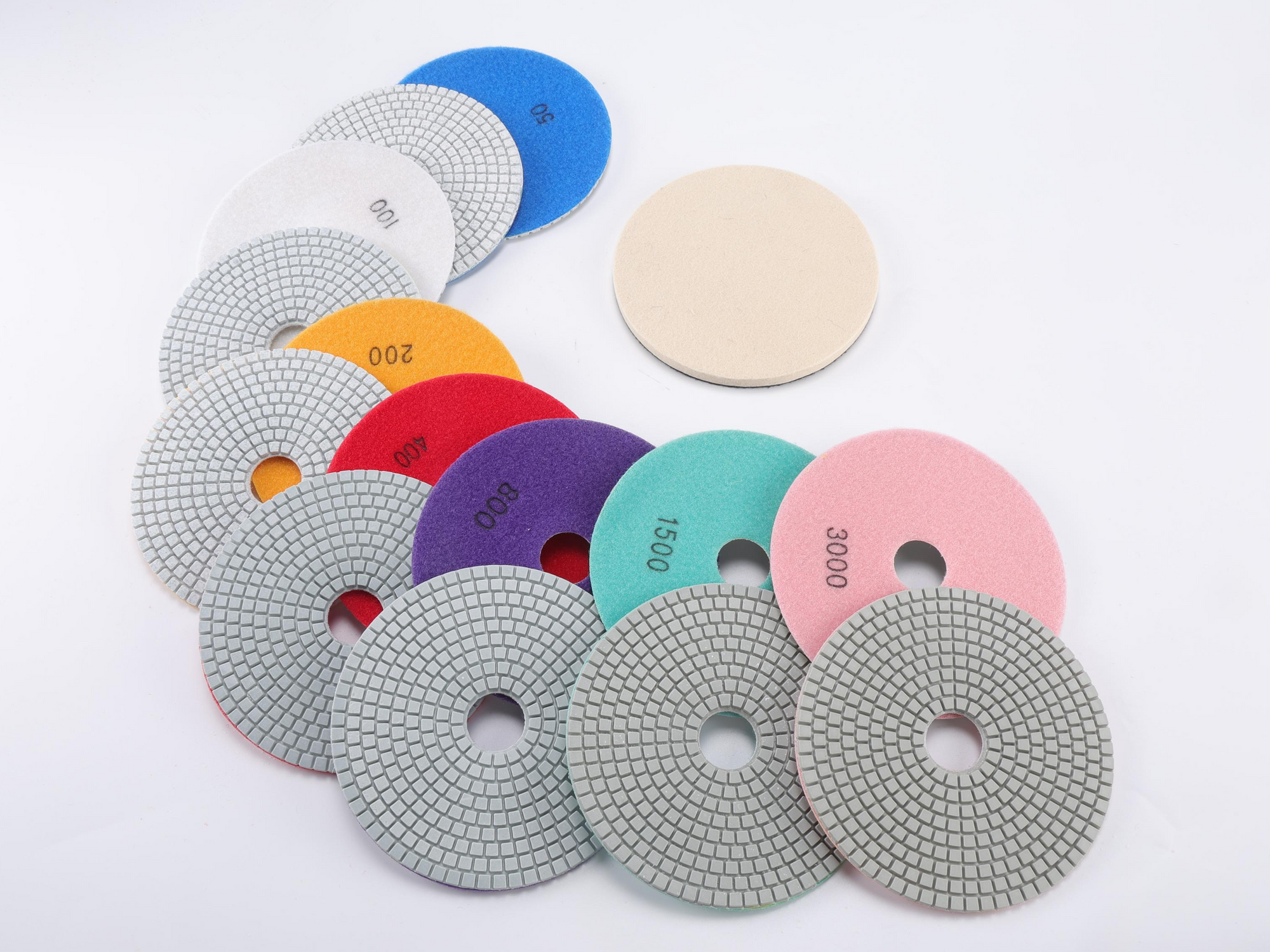